Laser Cutter - Wolverine
Laser Cutter - Wolverine | |
---|---|
![]() | |
Name | Wolverine |
Zone | Laser Cutter |
Reservation Address | Link |
Reservation Calendar URL | Link |
HOWTO Reserve Time on Equipment | |
Owner | Roger Slykhouse |
Make Model | |
Part Number | |
Date Acquired | 2012-09-XX |
Storage Location | West wall, you can't miss it. |
Authorization Required | Yes |
Status | Running |
Value | 6500 |
IP Address | 10.13.107.223 |
MAC Address | ec:fa:bc:00:a0:dc |
Power Requirements | 240V Single Phase |
Documentation | The setup manual, File:OPERATIONAL MANUAL OF MACHINE xin USB.pdf is worth reading, if only for a laugh.
Inside the cutter, a Leetro MPC6515 control board coordinates the motors and laser firing. Its documentation is freely downloadable. So much grief has arisen from the awful state of the documentation and software, that an entire Chinese laser support forum has arisen for the hapless owners of these machines help each other. |
Other References | Good sources of info: |
Contents
- 1 Intro
- 2 Rules
- 3 Instructions
- 4 Damage Prevention
- 5 Maintenance Info
- 6 FAQ
- 7 ToDo
- 8 Authorized Users and Trainers
Intro
This is the older of the big laser cutters in the space. It has a 1200mm x 900mm bed and 150 watt tube. This one is named Wolverine because it's yellow and navy blue (or Maize and blue if you're a diehard UofM fan).
Rules
- You must be authorized to use either Laser Cutter.
- You obtain authorization by attending 2 training sessions, each with a different trainer.
- Your first training you will mostly be an observer while someone demonstrates the user of the laser cutter.
- Between your first and second training, you are expected go over these wiki pages and any relevant documentation, and to prepare a file for cutting.
- For your second training, the trainer will be your "co-pilot" while you "drive".
- To obtain training contact an authorized trainer. Training is usually done in ad hoc classes whenever someone needs training. Ask in #laserzone on Slack or contact a trainer directly by email or text.
- List of trainers is at bottom of this page.
- Each training session will take about 1-2 hours. And scheduling issues mean that members reasonably able to come to i3 should expect to be able to schedule both sessions over a few calendar weeks.
- DO NOT cut or engrave any material listed as BANNED on the Laser Materials List
- DO NOT cut or engrave any material that is not listed at all on the Laser Materials List. Ask the zone coordinator ahead of time.
- If you don't know what a material is, DO NOT cut or engrave it. Ask the zone coordinator to help you identify it.
- There is a consumables fee for this machine of $0.25 per minute (or $15 per hour) of laser-on time. This is to replace consumables, especially the expensive bulb. Check the display on the machine right after your job completes to get the time it ran. There is a wooden donation box for cash payments or you can use the paypal link in the infobox on this page.
- A reservation system is currently used for Wolverine. Cyclops does not. See HOWTO Reserve Time on Equipment for details.
- Do not change any settings on the LCD panel that you don't understand, and always reset the setting to how you found them when done. Some of these settings can cause major problems for other users if they are not reset. For example, logical origin, test fire time, etc.
- Guests may be trained and authorized to use Wolverine, but they must be accompanied by another current member who is also authorized to use Wolverine.
Reservations
Instructions
Cutting Dimensions
- Get material that will fit on the bed of the laser.
- Wolverine has a nominal cutting bed size of 1200mm x 900mm
- The recommended effective cutting bed size is 1190mm x 890mm (we've had reports of issues right at the edges)
- There is about 200-300mm of space outside the cutting area available for overhang
- There are other alternatives possible for even larger pieces using the pass-through - if you have a need please contact the laser zone coordinator to discuss.
- In case anyone needs to know the whole interior of the bay for some reason: there is 51 inches of clearance between the two rails the gantry runs on (the same width as the machine's bay door). 51 inches is also the measurement from the front lip to the back wall of the machine, but the door itself takes up 3/4 of an inch of that.
Choosing Materials
The laser cutter can cut or etch a wide variety of materials. However some are not possible to cut with our current set-up, and other materials are dangerous - they release fumes that damage humans or the laser cutter itself. There are some materials that cannot be cut, only etched.
You are responsible for knowing exactly what your material is before you try to cut it. DO NOT cut any of the banned materials. You are liable for expensive damage to the machine or worse - you may release toxic fumes that could easily harm or kill!.
DO NOT CUT
- Materials that contain a high proportion of glue (such as particle board)
- Plastics (or any other materials) that contain chlorine (such as all varieties of vinyl like PVC).media:LaserProcessingGuide_Plastics.pdf A trace amount of chlorine, such as found in the glue in thin plywood or the resin of medium density fiberboard, is acceptable. Particle board has too much glue. You are responsible to know whether there is chlorine in your material before you try to cut it.
- "Plexiglass" - please be sure that it is acrylic and not polycarbonate. Look along the cut edge of the material, from the side. Polycarbonate is dark on this area; acrylic is light. Polycarbonate is one of the most dangerous materials you could try to laser. It instantly starts producing yellow, acrid, toxic fumes which will corrode your lungs, and the mechanisms and lens of the laser. When the lens clouds up with these fumes, it may reflect the laser back into the machine, which may melt the head and set the machine on fire. You may not be able to reach the fire extinguisher due to what is in your lungs. Both these outcomes will upset the community.
- PTFE (Teflon) will release Fluorine gas, which when inhaled by humans causes flu-like symptoms, and when mixed with hydrogen (in the atmosphere) will create hydrofluoric acid. This is corrosive and will fog up the optics of the laser.
Most dense materials can normally be cut up to about thicknesses of 3/8 to 1/2 inch in a single, slow pass. Some thicker materials can be with multiple passes. The thickest that can be practically cut through is about 1 inch (or 25 millimeters), since the focal point of the laser is just a little more than half an inch below the nozzle. You will have to get creative to cut anything thicker, such as cutting half way through, flipping the object over, and perfectly realigning it to cut from the other side.
Material | Cut? | Etch? | Mark? | Notes |
---|---|---|---|---|
ABS Plastic |
BANNED |
BANNED |
BANNED |
Warps. Decay products contain a wide range of toxins, including: cyanide, đˇ methyl styrene, phenol, phenyl cyclohexane, and benzene derivatives |
Acrylic (Plexiglas, PMMA) | Yes |
Yes |
Yes |
for cutting 2mm (300 speed, 100 power, corner 50) |
Basswood 3/16" | Yes | Yes | Yes | cut 30, corner 20, speed 120 |
Carbon fiber (uncoated) |
Yes |
Yes |
Not recommended |
Coated carbon fiber may contain epoxy resin (which see) |
Ceramic | No |
Yes |
Yes | |
Cloth (see comments) |
Yes |
Yes |
No |
See specific material, as some may be unsuitable (NPI) |
Chipboard |
Yes |
Yes |
Yes |
for cutting 1-ply (120 speed, 100 power, corner 50) for scoring 1-ply (160 speed, 30 power, 20 corner) |
Cork |
Yes |
Yes |
Yes |
|
Delrin (acetyl) |
Yes |
Yes |
Yes |
Not recommended due to toxic gases. Will melt and resolidify, so prompt removal is recommended. |
Epoxy |
BANNED |
BANNED |
BANNED |
Gas byproducts are highly toxic |
Fiberglass |
BANNED |
BANNED |
BANNED |
|
Glass | No |
Yes |
Yes |
|
HDPE (high density polyethylene) |
Yes |
Yes |
Not recommended |
Makes a big gooey mess |
Human flesh | BANNED |
BANNED |
BANNED |
(yes, this has come up ) |
Kapton (polyimide) |
Yes |
Yes |
Yes |
Some carbonization at the cut edges |
Leather |
Yes |
Yes |
Yes |
ONLY natural leather; no synthetics! (see vinyl and PVC) |
Marble | No |
Yes |
Yes |
|
Masonite | See Tempered Hardboard | |||
Matte Board | Yes |
Yes |
Yes |
|
MDF | Yes |
Yes |
Yes |
Speed 10, Power 100, Corner Power 50 to cut 1/4" material |
Melamine | Yes |
Yes |
Yes |
|
Metals |
Yes |
Yes |
Yes |
Very thin (>0.02 inch) steel can be cut at speed 1-2, power 100, 40 psi shop air assist |
Metals - Painted |
Yes |
Yes |
Yes |
See Metals. |
Model Foam |
Yes |
Yes |
Maybe |
(expanded polystyrene) |
Mylar |
Yes |
Yes |
No |
|
Nitrile (NBR) |
Not recommended |
Yes |
Not recommended |
|
Nylon (polyamide) |
Yes |
Yes |
Yes |
Fabric edges melt, reducing fraying |
Particle board |
BANNED |
BANNED |
BANNED |
Not the same as MDF. Glue may produce toxic byproducts. |
Paper |
Yes |
Yes |
No |
Speed 400, Power 30, Corner Power 16 to cut bristol board with high resolution (small kerf) Speed 200, Power 30, Corner Power 16 to cut bristol board with low resolution-across long edges |
PLA (PolyLactic Acid) |
Yes |
Yes |
Not recommended |
Like Delrin, may melt and resolidify, so remove promptly. Watch for green flame color on a test piece due to pigment or additives. If present, stop and avoid that color. |
Plywood |
Yes |
Yes |
Yes |
We've even recently had success with 3/4" birch plywood at speed 2.5, power 100, 20 PSI. though better luck might be had with lower power, higher speed, and several passes. |
Polycarbonate (Lexan, Plexi, etc.) |
BANNED |
BANNED |
BANNED |
Does not cut well, with discoloration and charring. Produces toxic fumes and a strong, unpleasant odor. |
Polyester (resin) |
Yes |
Yes |
Yes |
|
Polypropylene | Yes | Probably? | Not sure | |
Polystyrene sheet | Yes | Yes | No | Also known as Styrene, and used in the Vacuum Former. The 0.03" sheets cut easily at speed 50, power 100, corner power 60. |
PTFE (Teflon) |
BANNED |
BANNED |
BANNED |
Cuts well, but can produce fluorine gas |
PVC (Polyvinyl Chloride) |
BANNED |
BANNED |
BANNED |
see above |
Records (aka 'Vinyl' aka PVC) |
BANNED |
BANNED |
BANNED |
see vinyl, below |
Rubber (non-chlorine containing) |
Yes |
Yes |
No |
Make sure it does not contain chlorine |
Tempered hardboard |
Yes |
Yes |
Yes |
|
Tile |
No |
Yes |
Yes |
|
Vinyl or PVC of any kind |
BANNED |
BANNED |
BANNED |
Produces chlorine gas which is poisonous and corrosive to the machine |
Wood, veneer |
Yes |
Yes |
Yes |
|
Wood, natural |
Yes |
Yes |
Yes |
|
Wood, Plywood, Birch - 1/8" thick |
Yes |
Yes |
Yes |
Cut - 40 (First pass, minimal char, some stray strands.) |
Anything not in this list |
BANNED |
BANNED |
BANNED |
If you think it's safe, ask the zone coordinator for approval. |
External references on laserable materials
- Cutting vinyl: bad idea!
- Cutting PVC, Lexan, polycarbonates: bad idea!
- List of what can and cannot be cut, and some notes about each.
- How to identify polymers in your material through burnination.
- Laser Cutter Materials from ATX Hackerspace
- Bad materials for laser cutting
- Common laser cutting materials
- Best plastics for laser cutting
Getting your design ready
You will need access to vector graphics software to design your parts. So far, DXF files seem to work the least-bad of the various vector filetypes, so use them. LaserCut is good for putting finished art into the laser, but barely adequate for designing art. Popular vector graphic programs for making designs are Inkscape, Adobe illustrator, and Fusion360. Inkscape is free and is on the Wolverine PC. Illustrator is not free, but is available for i3 members to use in the Media Lab. Fusion360 isn't free software but they do have a free hobbyist license that has some limitations but the limitations are more minor inconveniences than show stoppers. If you need help preparing a file, just ask on Slack.
Using LaserCut software
Setting up the software on your personal laptop (Optional)
Importing vector graphic files
Basic design set-up
Sending your file to the laser cutter
Setting cutting speed & power
See the Materials List for material-specific parameters
In general:
- The 2 main settings for cutting are speed and power.
- If your material isn't cutting through, decrease the speed and/or increase the power. (after checking that everything is set-up/aligned properly)
- Lower speeds allow for lower cutting power, which saves life on the laser tube.
- Lower speeds also cut a wider "kerf" (thickness of cut) through the material.
- At higher speeds the cut is faster but requires higher power, which uses up the laser tube faster.
- Corner power should be set below to the regular power to reduce the power going around a corner. This makes up for the fact that the laser decelerates around the corner for better control. (Lower speed at the same power would result in a higher effective power in the corners otherwise, making the corners look bad).
- High power on wood and paper may cause some discoloration near the cuts (browning color from burned material).
Time-of-cut Checklist
- Lift the fire extinguisher and set it back down. This verifies that your muscle-memory knows where it is.
- Make sure there is nothing obstructing the path of the laser head toward the right rear of the working surface if the head isnât already there.
- It will move there as soon as you turn on the laser.
- Press the silver power button on the laser, and wait for it to boot and auto-home.
- The chiller, laser exhaust fan, and air compressor should all turn on when the laser turns on. You should hear the chiller beep and the noise of the exhaust fan. (If this does not happen, see âSteps for manual overrideâ at the end of this list.)
- Ensure the exhaust blast gate is open on the back of the laser cutter. Slide the door all the way open (toward you).
- If the other laser is not in use, close the blast gate at the back of the other laser to increase the exhaust flow.
- Place material (square to edge of honeycomb or gantry).You can also run the head left / right and watch the red dot to see if it moves parallel to the edge of the material. Adjust alignment as needed.
- With the D-pad, jog the head over to center of material.
- Look for fogging or damage to each of the three mirrors. This may require a light to see the mirror in the focus turret. While looking in there, look for specks or fogging of the lens.
- Check the mirrors for debris, and clean if necessary. âââONLYâââ use lense cleaner and microfiber lens cloths to clean mirrors. Paper towels will ruin them. If you are unsure, ask someone for help.
- Press "Z" to enter the mode to raise or lower the bed.
- Set the focus with one of the acrylic manual focus gauges.
- Press "Z" again to exit Z mode. (ESC will not exit this mode)
- Make sure the yellow manual air valve on the wall is open (parallel to the pipe).
- Make sure "Blow" is enabled in the Cut or Engrave options dialog in LaserCut for each layer in your design. (Next to power and speed.) For cutting, use "Always blow". For engraving, use "Blow".
- Download your design from LaserCut software to the laser cutter.
- With the D-pad, jog the head to start of your cut. Remember that the blue dot in laser cut tells you where the laser assumes you have placed it.
- Keep one hand over the emergency-stop while using the "Test" button to check boundaries.
- Close the hood, if it's open. The laser will not fire if the hood is open.
- Press "Start".
- âââDO NOT WALK AWAYâââ. See the writeup of Thinkhaus's laser fire for why.
- When the laser cutter finishes, observe the elapsed time on LCD and put money into box.
- Remove all material, scrap, and cutouts from the laser bed. Please leave it clear for the next person.
- Press the silver power button to turn off the laser cutter. The chiller should automatically turn off. The exhaust fan should also turn off if the other laser cutter is not in use.
- Since the air compressor is shared across the whole space, it will not be turned off automatically. Check to make sure that nobody in the space is using anything that requires compressed air. If not, then turn the air compressor off with its physical power button.
Steps for Manaul Override
In the unlikely event that there is a problem with this automation system, there are manual overrides in place to turn everything on.
- The air compressor can be turned on with its physical power button.
- The exhaust fan can be turned on via a black and orange box with a white button on the wall next to Cyclops labeled âLaser Exhaustâ.
- The chiller can be turned on with the small black button on the white âSonoffâ module that is on the top front of the chiller.
How to use the manual focus gauge
The manual focus gauges are in the laser cutter box. They are small L-shaped pieces of acrylic with "69mm For use with 63mm lens" engraved on them, corresponding to the 63mm focal length lenses currently installed in the laser cutters. To check the focus, place the gauge on the surface of the material you are cutting. The underside of the nib should rest against the top of the knurled fitting, as shown in the pictures to the right.
To re-cut the manual focus gauge, or to modify the file for a different lens, use the File:63mmLensGauge.dxf (DXF file) or the File:63mmLensGauge.ecp (ECP file).
Damage Prevention
Be very careful when removing the emergency stop, because it homes itself during every power-on. So, be sure the lens head is free. If the table is so high that the head is stuck in the honeycomb, open the lower doors of the laser, manually pull the belts on the screws so that the bed goes down. After this, this procedure will have to be reversed, measuring the distance from both sides of the bed to both sides of the gantry.
Coolant failure will destroy the laser, so see the status lights to make sure the chiller is running.
Be sure the exhaust is on by checking the status lights, or the smoke gathering in the machine will damage the mechanics, the optics, and any nearby humans.
Never laser-cut polycarbonate. It is highly flammable, and will produce toxic, highly corrosive smoke. Also do not cut plastics containing chlorine, like PVC (Vinyl).
If material catches on fire, hit the emergency stop, yell "fire", and use the fire extinguisher mounted to the front of the laser. Pull the pin, and spray carbon dioxide gas in a sweeping motion over the flames. It just dispenses carbon dioxide gas, not foam. This will do no damage. It's just loud.
Maintenance Info
The glass should be cleaned regularly, and the screw drives for the Z-axis should be checked for lubrication.
Calibration
Calibrating the three mirrors keeps the beam aimed through the center of the lens, which improves beam efficiency.
We have a small wire crosshair in the small laser equipment bin on the laser work bench. It attaches in front of a mirror in the path of the beam, and has a slot to hold a slip of paper. Use the gantry to move the lens assembly to the four corners of the bed. In each corner, fire the laser beam into a piece of paper in the crosshair. The differences in these four pieces of paper will show you the direction in which the mirror's angles need to be adjusted. Use the thumb screws to adjust the mirrors. Observe the resulting change by repeating the process of firing the beam into a paper.
Cleaning the laser head
If speed for CUT in 1/8" MDF falls below 20,then check the focus and have a trainer clean both mirrors and lens.
Trainers:
- Use alcohol from the laser box and cotton ball.
- The convex lens side goes toward the laser.
- The capture ring tool is in the white box.
- Use tweezers for removal of o-ring.
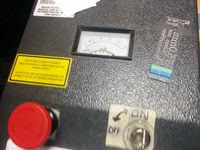
(Very Incomplete) Maintenance Log
8/10/2018 - Replaced 120mm 120VAC fan with 240VAC fan, disabled the built in 120V outlets, and plugged machine into 240VAC from the bus bar.
Sources for Replacement Parts
Sector67 suggested http://www.ebay.com/usr/strut-your-stuff-here part #NP1190-150
FAQ
- If I have a jpeg file, how do I etch it on a piece of acrylic?
- The easiest way is to import the jpeg file into the LaserCut software, then put it on an engrave layer. This will not be a grey-scale engrave, it will just be black & white.
- If I set speed on LaserCut, what does the SPEED % mean on the display of the Laser Cutter?
- The speed on the Laser cutter screen is irrelevant. When uploading files manually (Without the LaserCut software) this is where you change your speed/power. However, LaserCut handles all of this for you, and the cutter will follow your settings from the program, regardless of what they are set for on the cutter itself.
- I have a jpeg of a line drawing. How can I cut a piece of acrylic using that line drawing?
- It is recommended that you upload the image into a vector art program (ie: Illustrator, Inkscape) and trace the into tool paths. If you try to cut the jpeg directly, the cutter will also try to cut the artifacts in the image and not only extend your cut time, but also create the potential of ruining your image.
- Do I need training to use the Laser Cutter? If so, how do I get it?
- Yes, see the Rules section of this page for training information.
- Why do we have 2 Laser Cutters?
- Current answer - the lasers are one of the most frequently used zones. Multiple people often want to be working at the same time, sometimes running longer jobs. Also, the older lasers needed frequent repairs, so having 2 lasers ensured more up-time for the zone.
- Historical answer - When the lasers were originally purchased, we received a huge discount by ordering multiple. (Three were actually ordered. The third is located with our friends, Sector67.) After the funds were raised for the actual purchase (via a kick-starter), one of our members contributed the funds necessary to purchase all three units. As a result, Bumblebee was owned by the space, Wolverine is owned by Roger S., and the third was purchased/is owned by Sector67 in Madison, Wisconsin.
- LaserCut is demanding that the dongle be re-installed, even though the dongle is plugged into the normal laser cutter laptop! How can I fix it?
- Make sure the USB hub with the dongle is plugged into the side port, not the back port, of the laptop. Windows XP is apparently picky about which USB port drivers are installed to.
- How can I tell how much my job is going to cost?
- The best way to estimate cost is to run the job on the machine with the power set to 0. Unless you're doing something really complicated, the laser time probably won't cost you more than a few bucks. Some people try to use the LaserCut software to estimate cost based on path length, but there are many complications with this method. The laser will decelerate around corners and curves, so the head speed is not constant. Since we charge based on total run time as measured on the machine's UI, which includes the non-cut transits, path length means effectively nothing.
TroubleShooting
- Power won't come on, or shuts off during use.
- Check the other items on the same line, such as the laser computer or the overhead light. If they work, make sure the laser is still plugged in. If the power is off to the whole line, the breaker box is located in the back corner in the wood shop. Flip it back on, and you should be good to go. (This is a known issue, and a more permanent fix is being discussed. Until then, apologies for ruined cuts)
- When running TEST I get a SOFT STOP message on screen and no test.
- That usually means your cut runs off the laser table. Check your origin point on the file and where you have the laser head starting. Sometimes it means that Logical Origin is set to ON which places your cut off the table, no matter where you have manually set the laser head.
- How can I turn off Logical Origin?
- To Cancel Logical Origin use the keys on the Control Panel on the Laser and the Control Panel Display.
- Hit ESC 3 times.
- Hit the RETURN key (the one with an arrow that goes down and to the left). This should highlight the current file name.
- Hit RETURN again. This should pop you to the Logical Origin screen.
- Hit Right Arrow until the field Cancel Logical Origin YES is highlighted.
- Hit RETURN.
- My Test doesn't start where my laser head is and I have turned Logical Origin off
- Make sure to check the IMMEDIATE box and save before Downloading AND turn off Logical Origin to allow the origin to be the manually set position of the laser head.
- This could also mean your cut is running off the table, or close to the edge.
- My file cuts/engraves multiple times
- In the layer box in LaserCut, scroll right and make sure "Times" is 1.
- On the control panel, the bottom row should show 001 next to PIECES. If it's another number, press Menu, ESC, Right 4 times, and then Up/Down to set the number to 001.
- It takes several minutes or infinite minutes to compile in LaserCut
- This has happened with some (but not all) DXF files from OpenSCAD. Open the dxf file in CorelDraw and then save it as dxf. It will "clean it up" and your compiles will now be very quick.
- When cutting 1/8mdf through it takes 100% and slower than 20 speed.
- Check Focus. If problem persists have trainer clean lens and mirrors. DO NOT attempt cleaning if you are NOT a trainer.
- When downloading file to laser cutter, no file appears in the DownLoad window or on the laser cutter
- Your file is too big (some combination of actual size and complexity of design) to be transferred via the cord. You can download your design directly to the laser cutter via USB flash drive.
- In the LaserCut Download window, choose "Export file" instead of "Download Current"
- Find the files, a .mol and .txt and put them on a flash drive. They don't need to be the only files on the drive, but probably should be the only .mol file
- Plug the flash drive into the laser cutter USB port. The port is located on the right side of the laser cutter, about 2 feet off the floor near the front edge. (someone should add a picture of the port location)
- The file will be downloaded automatically- it might take a while to download, but it'll give you the progress as it goes.
- Proceed as normal- you should see the name of the file in the menu as usual.
- The laser head moves through the design, but the laser doesn't fire!
- Laser power setting in LaserCut should be above 17.
- Check the air nozzle to make sure it isn't knocked out of whack and blocking the laser path. Check the mA meter just above the control panel. If it jumps up around 10-40 mA, then the laser supply is firing and just getting blocked
- Make sure the chiller is on (safety interlock) by checking the status lights
- Make sure the door is all the way closed. The door interlock uses a small magnetic sensor on the front right bezel into which the door sits when closed. The magnetic sensor requires a small gap between it and the magnet. If the door requires re-alignment, TELL A TRAINER. DO not try to fix it yourself, just let someone know to re-align it so you don't make it worse.
- The laser turns on but doesn't start up. Screen says "System is starting. Please wait."
- Let the zone coordinator know that this happened.
- There is a problem with the laser cutter's mainboard firmware. It probably needs to be reflashed. Instructions for how to do this:
- There is a white USB drive labeled "Bumblebee Firmware" in the laser maintenance drawer. ONLY USE THIS IN BUMBLEBEE
- Turn the laser off.
- Insert the USB drive.
- Turn on the laser.
- Wait 2 minutes.
- Remove the USB drive.
- Restart the laser.
- It should start up correctly now. If not, tell the zone coordinator.
ToDo
- Develop a list of materials, with speed and power settings for various cutting depths.
- Add bumpers under the lid.
- Add stringer gas shocks so the lid does not slam shut.
Authorized Users and Trainers
Trainer Name | Certified Date |
---|---|
Matt Arnold | 2013/08/20 |
Roger Slykhouse | 2013/08/20 |
Mike Fink | 2015/02/20 |
Matt Huber | 2013/12/03 |
Lewis Dennison | 2018/09/11 |
User Name | Authorized By | Date of Most Recent Training |
---|---|---|
Kevin Flory | Devon Truscott | 2013/08/20 |
Jamie Burdeski | Devon Truscott | 2013/08/20 |
Mike Fink | Devon Truscott | 2013/08/20 |
Marie-Therese Enga | Devon Truscott | 2013/08/20 |
Eric Merrill | Devon Truscott | 2013/08/20 |
Brian Wennberg | Devon Truscott | 2013/08/20 |
Jessica Rowland | Devon Truscott | 2013/08/20 |
Amelia Meyer | Devon Truscott | 2013/08/21 |
Jim Kemp | Roger Slykhouse | 2013/08/22 |
Brace Stout | Devon Truscott | 2013/08/23 |
Derek Kuschel | Devon Truscott | 2013/08/23 |
Steve Nowicki | Roger Slykhouse | 2013/08/26 |
Greg Smith | Devon Truscott | 2013/08/20 |
Devin McPherson | Nate Bezanson | 2013/09/07 |
Adrienne Johnson | Devon Truscott | 2013/10/22 |
Thomas Shui | Terry Wynn | 2013/11/07 |
Matthew Huber | Nate Bezanson | 2013/12/03 |
Rob Lifton | Nate Bezanson | 2014/02/04 |
Joe Bender | Amelia Meyer | 2014/07/19 |
Matt Gardeski | Amelia Meyer | 2014/08/22 |
Ken Siegner | Nate Bezanson | 2014/09/14 |
Lewis Dennison | Nate Bezanson | 2014/10/27 |
David Henry | Nate Bezanson | 2014/12/19 |
Justin Triplett | Mike Fink | 2013/08/20 |
Konrad Brown | Mike Fink | 2015/03/03 |
Brad Tarratt | Mike Fink | 2015/04/03 |
James O'Dell | Mike Fink | 2015/05/24 |
Alec Beardsley | Matt Arnold | 2016/03/11 |
Matt Arnold | Roger Slykhouse | 2013/08/20 |
Terry Wynn | Roger Slykhouse | 2013/11/20 |
Roger Slykhouse | N/A | 2013/08/20 |
Sean Work | Matt Huber | 2018/01/11 |
Ben Seiber | Matt Huber | 2018/01/11 |
Drew Jackson | Kirsten Hellmer | 2018/01/21 |
Carlos Sola | Kirsten Hellmer | 2018/01/21 |
Gary Grzebienik | Kirsten Hellmer | 2017/01/21 |
Carlos Sola | Kirsten Hellmer | 2017/01/21 |
Alex Vincent | Matt Huber | 2018/04/12 |
Tom Nardone | Mike Fink | 2017/3/15 |
Alicia Chatman | Matt Huber | 2018/06/14 |
John Coggeshall | Matt Huber | 2018/06/14 |
Ari Schweyen | Matt Huber | 2018/09/12 |
Peter Botros | Kirsten Hellmer | 2018/09/15 |
Arthur Mize | Lewis Dennison | 2018/12/17 |
Mara Furland | Mike Fink | 2019-02-03 |
Evan Allen | Mike Fink | 2019/01/19 |
Matthew From | Mike Fink | 2019/02/12 |
Brian Maynard | Kirsten Hellmer | 2019/02/02 |
Kam Watson | Lewis Dennison | 2019/10/10 |
Michael Bereczky | Mike Fink | 2021/01/09 |
Zack Sutton | Mike Fink/Roger S | 2022/03/02 |
Freddy Neumann | Roger S/ Lewis D | 2022/08/10 |
Alex Taylor | Lewis D/ Roger S | 2022/08/16 |
Andrew Lanagan | Roger S / | 2022/11/18 |
Alex Tauber | Roger S / | 2022/11/18 |
Neil McEachin | Roger S / | 2022/11/18 |
Megan Greenwood | Roger S / | 2022/11/18 |
Sabrina Good | Roger S / | 2022/11/18 |
(prefer Aria) - Sean Kelly | Roger S / | 2022/11/18 |
Sophia Tsuker | Roger S / | 2022/11/18 |
Greg Good | Roger S / | 2022/11/18 |
Petur Gislason | Roger S / | 2022/11/18 |
Deb Scott | Roger S / | 2022/11/18 |
Amy Hang | Roger S / | 2022/11/18 |
Sabrina Good | Lewis D/ | 2022/12/1 |
Megan Greenwood | Lewis D/ | 2022/12/13 |
Frank Ahola III | lewis D/ | 2023/1/12 |
Tim Wainz | lewis D/ | 2023/2/15 |
Kevin Bastyr | Roger S/ | 2023/7/26 |
Estefany Velazquez | Roger S/Matt A | 2023/8/19 |
Paul Lee | Alec Beardsley | 2017 |
Emerson Craven | Roger S/ | 2023/11/10 |
Jim Craven | Roger S/ | 2023/11/10 |
Daniel Vitenson | Roger S/ | 2023/11/10 |
Lauren Yellen | Roger S/ | 2023/11/10 |
Steven Yellen | Roger S/ | 2023/11/10 |
Shauna Siso | Roger S/ | 2023/11/10 |
Will Kelly | Roger S/ | 2023/11/10 |
Benjamin George | Roger S/ | 2023/11/10 |
Carlos Cuartas | Roger S/ | 2023/11/10 |
Ahmed Safdar | Roger S/ | 2023/11/10 |
Scott Brandenburg | Roger S/ | 2023/11/19 |
Filip Kin | Roger S/ | 2024/01/19 |
Lou Wil | Roger S/ | 2024/01/19 |
Furqan Memon | Lewis/ | 2024/02/15 |
Brian Bezanson | Roger S/ | 2024/03/30 |
Adam Killeen | Roger S/ | 2024/03/30 |
Andrew j. Langan | lewis | 2024/05/21 |
Brian Bezanson | lewis | 2024/05/17 |
Lou Will | lewis | 2024/05/07 |
Hans Chen | lewis | 2024/05/07 |
Furqan Memon | lewis | 2024/05/01 |
J Montgomery | lewis | 2024/05/15 |
Thomas Anderson | Roger S/ | 2024/07/26 |
Thomas Burns | Roger S/ | 2024/06/28 |
Ravi Shah | Roger S/ | 2024/07/26 |
Andrew Youmans | Roger S/ | 2024/11/01 |
Ben Mick | Roger S/ | 2025/01/10 |
Jill Burdick | Roger S/ | 2025/01/24 |
Alex Williams | Roger S/ | 2025/01/24 |
Jeff Burdick | Roger S/ | 2025/01/24 |
Aj H | Roger S/ | 2025/02/28 |
Roger S/ | 2025/01/24 |